KSU maintenance training at the Barsebäck NPP
Human performance and Safety culture
Is it possible to train people to improve human performance? What is human performance and what is its connection to safety culture?
When we were given the task of creating the “Course in Safety Culture & Human Performance” these were the first questions we asked ourselves.
What are the answers? Unfortunately the first answer is no, you can’t train people to improve human performance. When you perform a job or a task, human performance is the combination of the behaviour and attitude you show while doing the work. Behaviour and attitude are something that you develop over many years under the influence of parents, friends, colleagues, life experiences, work environment, work conditions and so on. You could call it “everyday life learning.” You learn whether you like it or not and you don’t only learn good things. You might even learn things which, perhaps, result in bad behaviour.
So, we can’t train people to improve human performance, but what can we do in order to encourage it? Inspired by Chris Argyris (an expert in “single-loop” and “double-loop learning”) we created a one-week course designed to give participants exposure to different situations where attitude and behaviour can be observed and used as a basis for dialogue about what we can be learnt from it. Reflecting upon one’s experiences and communicating with each other were the tools we used to encourage the learning process.
To get as many perspectives as possible during a course we try to mix up the categories of participants taking part. For example, maintenance personnel from all three nuclear power plants in Sweden, electrical, mechanical and I/C personnel, juniors and seniors, craftsmen, engineers, managers and entrepreneurs, men and women all took part. The better the mix of participants you have, the better the results you achieve.
The course begins with different activities aimed at “establishing the group”. You won’t get a good dialogue with 10 to 15 people who haven’t met before. The participants will acquire a lot of experiences during the week, but we also want them to share experiences from their daily work. Each day starts with a time of reflection where experiences from the day before are discussed. This session is led by a facilitator.
At the end of the week participants are divided into a mechanical group, an electrical group and an I/C-group. Each group gets different jobs to do, which are done within the containment area. The scenario created is that the power plant has been started up again after an outage but because of a leaking steam valve it has had to shut down again. Before the start-up some jobs had to be done in the containment area. Different tasks were prepared in order to see how the maintenance personnel act. There was, for example, a job to be done with a pilot valve but the wrong valve had been tagged. Valves that should be closed (according to correct work procedure) were left open. Scaffolding covers the evacuation route. How do the personnel act? Do they notify the faults? Do they communicate with the control room? During this exercise we also observe how they allocate each kind of task to different members of the group, how they communicate between the different groups and how they cover open pipes to avoid foreign materials getting inside them.
Before the jobs start a pre-job briefing is given and after finishing their tasks a post-job debriefing is carried out. If something unplanned occurs personnel should use the STAR (Stop, Think, Act, Review) process. Self-checking and peer checking are other human performance tools that can be used.
The different jobs are quite easy to perform, but by putting them within a “minor fault” scenario, different situations can be simulated, assessed and discussed in order to learn from what the participants experienced. When something goes wrong we normally focus on a technical issue, but many times it’s all about human factors and human performance. After the one-week course we hope that participants have learned how to use this process of reflection and good communication as a tool to help them learn from different situations and experiences.
The practical and realistic methods that we used as a basis for this human performance and safety culture training helped us achieve a Good Practice rating following a 2009 OSART review.
Technical courses
As with all training you try to describe reality by using illustrations, photos, films, perhaps even mock-ups or simulations. The closer you get to reality the better. At Barsebäck NPP it is reality. To use a nuclear power plant for maintenance training is quite unique.
Training is based on task analysis made in collaboration with highly competent experts from Sweden’s nuclear power plants. The development of the course gives a possibility for an exchange of competences between experienced maintenance personnel and inexperienced staff – and all under strictly controlled circumstances. Since a lot of competent and experienced personnel are retiring there is an urgent need to transfer their knowledge to the next generation.
The technical courses focus on practical exercises by using systems, components and equipment in the facility. For example: disassembly and assembly of the reactor vessel before and after refuelling. The training is performed in a real environment led by experienced and skilled trainers. Students handle real components without any risk of effects on production or damage to the fuel.
The training takes place in the reactor halls at Barsebäck unit 1 and 2, without being influenced by any other activities and schedules. This provides a relaxed learning environment with space for reflection at different moments in the process. Even if it is a technical course you still have to make sure that there is time set aside to learn by reflecting upon and sharing experiences.
Background
History of KSU maintenance training
For political reasons Barsebäck NPP Unit 1 was shut down in 1999, and Unit 2 in 2005. During the lengthy period of political discussions it was considered - both in Barsebäck and at other NPPs - how Barsebäck might be used in a meaningful way after the shut-down.
Specifications for the provision of maintenance training were designed by a working group that represented Sweden’s NPPs. The participants also represented different technique disciplines (mechanical, electrical and I/C).
KSU (Kärnkraftsäkerhet och utbildning - or nuclear safety and training) was contacted in March 2007 and asked to develop and implement this training course. KSU was contacted because it is owned by the NPPs and was already running training courses for operational personnel.
The decision to start maintenance training at Barsebäck was taken at a KSU Board Meeting in May 2007.
The first recruits for the new organisation in Barsebäck were made in October 2007 and the first course was held in April 2008. The KSU unit working in this field is called Maintenance Training. Nowadays this unit (see below) also offers courses for field operators.
Maintenance training contributed to the achievement of Good Practice rating following an OSART review in February 2009 and another one in February 2010.
OSART stands for Operational Safety Review Team, an international team of experts that conduct reviews of operational safety performance at nuclear power plants.
What have we achieved so far?
We have developed and run Human Performance & Safety Culture courses. This course is the main reason why we achieved Good Practice rating following OSART reviews.
We completed the analysis, design and development of seven new courses, together with experts from the NPPs. We now also run these courses.
We have developed and run two courses for field operators (valves, pumps, heat exchangers and practical skills for field operators).
We run courses in plant knowledge management for different target groups.
We are in the process of developing a further 5 new courses.
Learning environment 24 hours a day
The courses are residential courses. Breakfast, lunch and dinner are served in the power station’s dining room. The students stay in the 40 private rooms that have been renovated to hotel standards. There is the possibility for leisure time activities close by. The main reason for this residential solution is that we strive to achieve learning throughout the day - whenever the students are awake.
Organisation
The Maintenance Training Unit is a unit of the Product Development Department of KSU. It is run by a manager, Jan Johansson, a training developer, five instructors and a ecretary/administrator. Other tutors/training personnel are recruited from Barsebäck NPP and from other Swedish NPPs, contractors and suppliers of equipment and components.
Cooperation with the NPPs (maintenance training)
Management Group
There is a Management Group that consists of Maintenance Department Managers from the NPPs. This Group decides upon strategic/policy questions concerning cooperation, activity plans and long-term development.
Training Board
In the Training Board there are NPP representatives from the respective Maintenance Department and Human Resources Department. The Board decides upon training targets and competence requirements for the various elements of the training programmes provided.
Customer meetings
There are four customer meetings at each NPP every year. Managers at unit and group levels from the Maintenance Department, together with people working in competence matters in the Maintenance and Human Resource Departments, take part in these meetings. The main subjects of these meetings are course requirements and the yearly plan.
Experts
Training is provided as a result of working together with experts from the NPPs and from consultant companies. We also work together with experts in course development and in course performance.
Facts about KSU
KSU has approximately 285 employees, with training units located in Barsebäck, Forsmark, Oskarshamn, Ringhals and Studsvik (Head Office).
Turn-over is 310 million Swedish crowns.
KSU has invested more than 1.5 billion Swedish crowns in 9 full-scale simulators.
KSU is owned by the Swedish NPPs.
The company is part of the Vattenfall Group.
Pictures taken during training courses
Disassembly and assembly of the reactor vessel
Lift training
Combimatic/Combitrol maintenance training
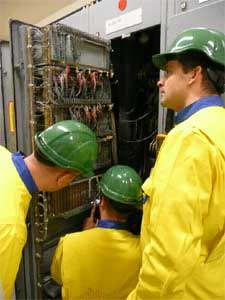
Human performance and safety culture
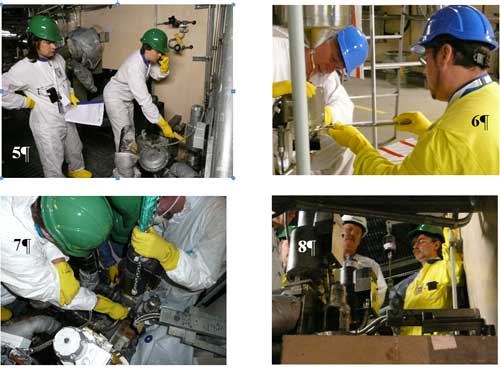
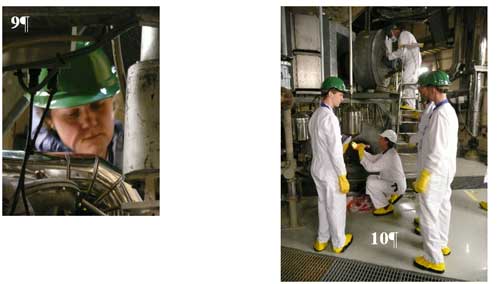
|