Some four hundred Boiling Water Reactors (BWR) and Pressurized Water Reactors (PWR) have been in operation for several decades. This concept the “High Pressure Boiling Water Reactor (HP-BWR)” makes use of the operating experiences todate. The HP-BWR combines the advantages and leaves out the disadvantages of traditional BWRs and PWRs by taking into consideration the experience that has been gained during their operation. The best components of both traditional reactor types have been retained and the more troublesome ones have been ommittedt. The main HP-BWR major benefits are as follows:
1. Safety is improved:
2. It is environmentally-friendly:
3. It is cost effective and simple:
-
It features a direct cycle, so there is no need for complicated steam generators
-
The moisture separators and steam dryers are inside the reactor vessel and additional separators and dryers can be installed inside or outside the containment
-
Well-proven simple dry containment or wet containment can be used
1. INTRODUCTION
Now the time has come to move a step further and develop an improved type of power reactor. Common sense, public confidence and economic considerations demand that this new design should not be a big leap forward from currently operating devices. However, it should be a significant improvement. Therefore, it is important to avoid those parts of the older designs which have caused trouble in the past e.g. PWR steam generators, BWR perforated reactor vessel bottoms, and instead rely only on a stable construction with proven components that have functioned well in the past. The HP-BWR (Figure 1) achieves these goals, by partly using the PWR concept, i. e. the pressure vessel, the electro-magnetic control rod operator, and by partly using the BWR concept, i. e. core internals, internal circulation pumps and steam and moisture separators. All the figures here are made by the combination of CAD models of existing BWRs and PWRs. The subject was introduced by the European Nuclear Society (ENS) as is outlined in References [1] to [4]
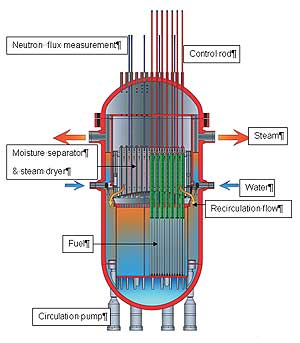
Figure 1, HP-WR
2. Safety is improved
The control rods are gravity-operated instead of being operated by an intricate hydraulic system. The gravity-operated control rod system has served well in PWRs. The stems are introduced into the reactor vessel via the vessel head (Figure 2).
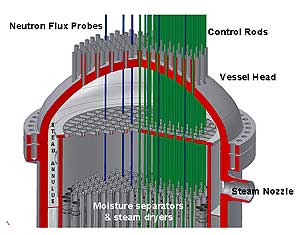
Figure 2, Vessel head
The control rods (Figure 3) themselves are cruciform, as is the case with BWRs. This assures large space for the cruciform rods between the BWR type fuel boxes. Also the neutron measurement sounds are introduced via the reactor pressure vessel head - once again as used in BWRs.
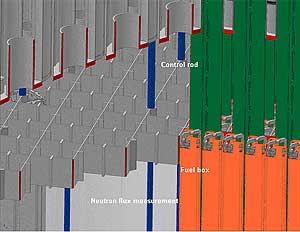
Figure 3, Control Rods
The bottom of the reactor vessel (Figure 4) is now smooth without numerous control rod penetrations, a great advantage compared with previous BWR designs.
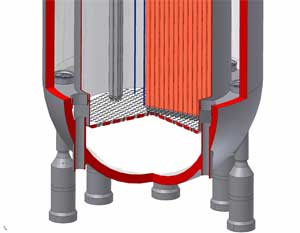
Figure 4, Bottom of the reactor vessel
All reactor vessel penetrations corresponding to different pipe connections are well above the top of the reactor core. This means that a major pipe break will not uncover the reactor core. Therefore a core spray system is not needed. In Sweden, for example, after receiving the approval of the safety authorities, the core spray system was removed in all internal pump BWRs were replaced by high pressure direct water injection in the Downcomer. Detailed studies of this subject are available at the Swedish Radiation Safety Authority.
Internal circulation pumps, located inside the reactor vessel and at the bottom of the Downcomer, are used to assure hydrodynamic stability. In this way, the orifices at the fuel channel inlets are chosen so that the single-phase pressure drop will dominate over the two-phase pressure drop and thereby avoid hydrodynamic oscillations. By utilizing natural circulation one could omit the circulation pumps altogether. However, the margin to avoid hydrodynamic oscillations may be reduced. This experience has been gained from several Boiling Water Reactors and is a phenomenon studied in thermal hydraulic loops at research institutes, universities and manufacturers
3. Thermohydraulic considerations
A thermal design criterion for a PWR reactor core is the limit of the fuel temperature (melting point of UO2 about 2800 °C), being the design temperatures 2000 °C at rated power and 2350 °C at a maximum linear fuel rating of 54 kW/m (see reference [5]). According to this criterion, recent PWR cores have an average linear fuel rating of 17.9 kW/m and maximum linear fuel rating of 44 kW/m. For a BWR, the maximum allowable temperature at the center of a fuel rod is 2500 °C in an emergency and 1850 °C during normal operation (see referemce [5]).
Following this criterion, a HP-BWR with a thermal power of ~2700 MW, and an electrical power output of ~1000 MW, may have a core with an average linear fuel rating of 13.6 kW/m and a maximum linear fuel rating of 44 kW/m. Without any fuel modifications, the temperature at the center of a fuel rod during normal operation is slightly higher and has been estimated to be 1885 °C. The maximum temperature of the Zircaloy-2 fuel cladding is around 491 °C, which is lower than the allowed maximum temperature of 550 °C.
A detailed comparison of the HP-BWR concept against modern PWRs and BWRs is given in Refence [5]
The HP-BWR has further advantages, namely improved thermal efficiency due to the higher temperature and further improved inherent stability due to the increased negative power reactivity coefficient. Table 1 shows a comparison - calculated with the RELAP5 (Mod3.3 Patch02) and PARCS codes - between a BWR and a HP-BWR. (see Table 1)
Table 1, Comparison between BWR and HP-BWR, calculated with the RELAP5 (Mod3.3 Patch02) and PARCS codes.
|
BWR |
HP-BWR |
Feed water temperature |
486.6 0K |
486.6 0K |
Outlet void temperature |
599 0K |
617.8 0K |
Pressure in the steam dome |
7 MPa |
15.5 MPa |
Inlet temperature to the core |
550.29 0K |
582.3 0K |
Inlet core quality |
-3.909E-02 |
-0.254 |
Outlet quality from the core |
0.128 |
0.323 |
Total Mass Flow Rate from the core |
13634 [kg/s] |
5955 [kg/s] |
Total Mass Flow Rate in the steam lines |
1795 [kg/s] |
2026 [kg/s] |
Total Mass Flow Rate through the pumps |
13634 [kg/s] |
5955 [kg/s] |
Total Power Coefficient |
-1.64e-4[Δk/%] |
-4.4e-4Δk/% |
The axial power distribution calculated with the RELAP5 (Mod3.3 Patch02) and PARCS codes, is similar in both types. See figure 5
Figure 5, Axial power distribution in HP-BWR and BWR, calculated with the RELAP5 (Mod3.3 Patch02) and PARCS codes
Ever since the onset of the nuclear power era, negative power coefficient has been considered a virtue, because it means that the reactor will close itself when there is a perturbation - even without the use of the control system. It is reassuring both for the nuclear engineer and the public that the security level of the reactor is satisfactory. After the out-of-control Chernobyl accident the value of the negative power coefficient was even more accentuated. The HP-BWR has a more negative power coefficient (pcm/%) than the traditional BWR and PWR.
At 150 bar the gradient on the saturated water density vs. saturation temperature curve (kg.m-3/0C) is steeper than at 70 bar (the derivative is more negative), resulting in a more negative moderator temperature coefficient (pcm/0C). See Figure 6.
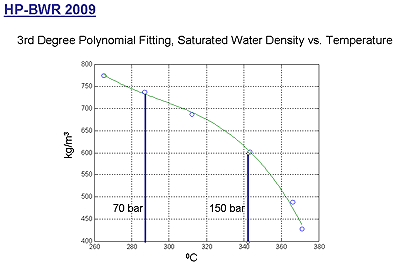
It is obvious that the gradient kg/m3/°C at 150 bar is steeper then at 70 bar
Figure 6. Saturated water density curve, the derivative is more negative at 150 bar than at 70 bar
The value of the negative void coefficient (pcm/%) is about the same for both types of reactors. However, the control algorithm for the pumps’ speed and for the control rods’ movement might need to be modified compared with a traditional BWR.
Thermalisation of the fission neutrons is successfully accomplished at 150 bars in the traditional Pressurized Water Reactors. PWRs contain not only water, at about a mere ~20 0C below saturation temperature, but also a lot of bubbles, due to subcooled boiling.
“Simple is beautiful” as 150 bar is far away from the critical pressure (~214 bar) the design is simple and thereby safer and more economical.
In Figure 7, the results of transient calculations made with the MATLAB code shows the HP-BWR’s long term stability without the use of any control system. BWRs are operated in an under-moderated condition and have, therefore, a strongly negative void coefficient of reactivity. This coefficient is a function of the core design, void location and void volume, which can be adjusted to an appropriate magnitude when the operating pressure is increased from 7 MPa to 15 MPa.
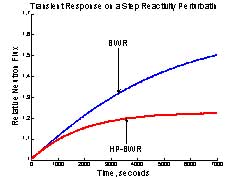
Figure 7: Long term stability without the use of any control system calculated with the MATLAB code (inherently stable reactor).
4. Environment friendly
Improved thermal efficiency is attained by feeding the turbine with steam at 343°C (~15MPa) instead of 286 °C (~7MPa). A rough estimate of the efficiency may be obtained through a calculation of the Carnot cycle theoretical efficiency (THot - TCold)/ THot. This gives for a BWR ~ 46 % and for the HP-BWR ~ 51 % at Tcold = 300 K, i.e. an increase by a factor of 1.109. Assuming the same improvement ratio, today’s efficiency of ~ 33 % would increase to ~ 37 %, which is supported by the analysis that follows on from the Rankine cycle efficiency (see Reference [5]).
The same results are obtained with a separate Rankine cycle calculation which is given in Reference [5]. This underlines the advantage of the HP-BWR, which uses the fuel more efficiently and releases less warm cooling water to the environment per produced kWh and, consequently, produces less waste. There are several conventional thermal power plants with 15 MPa turbines.
5. Cost effective, simple
The HP-BWR operates in direct cycle mode, with no need for complicated and expensive PWR steam generators. Furthermore, instead of the rather complicated BWR reactor pressure vessel bottom, a more simplified one is used. The main steam separators are inside the pressure vessel and secondary separators and dryers can be installed outside the reactor vessel, inside or outside the containment. The containment can be a simple dry containment (Figure 8) which allows easy entrance and inspections and also minor repairs during operation.
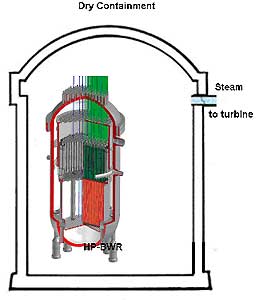
Figure 8: HP-BWR in a dry containment
Naturally the HP-BWR fits into a usual wet containment environment too. Also, when considering the refurbishment of an old BWR the HP-BWR fits the picture well. Se Figures 9 and 10.
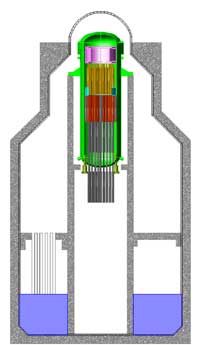
Figure 9. The closed Barsebäck BWR
There has been a suggestion to refurbish Barsebäck with a HP-BWR, which received the aproval of the Swedish and Danish people.
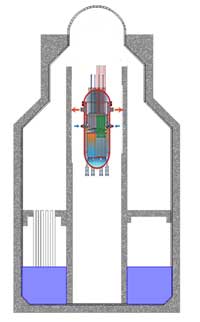
Figure 10. Proposal to refurbish Barsebäck with a HP-BWR
6. Conclusions and discussion
In this report a concept of a High Pressure BWR has been put forward that combines several advantages while avoiding some of the weaknesses of conventional BWRs and PWRs. This has been discussed and analyzed. However, some clarifying remarks should be added to complete the analysis.
The author is convinced that the experience gained during so many years of operating conventional light water reactors constitutes an unprecedented source of knowledge that new reactor concepts lack to a large extent. Conventional light water reactors may still be redesigned and optimized based on this knowledge, and the present concept provides a clear example of just such a possibility. Knowing how the different materials behave under prevailing reactor conditions and how to design the different components (the reactor vessel, the control rods etc.) from a structural mechanics point of view are examples of the advantages offered by using a reliable technology.
The HP-BWR concept also implies higher pressure and temperature for the turbine-generator plant then for the traditional BWRs and PWRs. Modern conventional thermal power plants with supercritical steam/water conditions (25 MPa and 560 °C) are generally employed. This indicates that the possibility exists of developing a steam cycle that could fit the steam conditions delivered by the HP-BWR.
Finally, one question remains to be answered - why has this concept of increasing the pressure and temperature of a BWR not yet been considered by the industry? Industry’s interest in lowering costs by increasing the total power of the reactor, rather than by increasing its efficiency, may have played a part in this issue. Probably in the past it was thought that an efficiency increase did not justify the necessary design and licensing effort. Now, with increasingly demanding environmental requirements the industry may be willing to reconsider this alternative.
Acknowledgements
Thanks to Hernan Tinoco and Karl–Axel Bartholf of the Forsmark NPP for the CAD models and to Tomasz Kozlowski and Joanna Peltinen of KTH for the RELAP and PARCS calculations
IAEA
I would like to thank the IAEA for the opportunity that was given to me - as a reactor inspector on leave from Sweden – to become an IAEA employee and to participate in IAEA’s OSART and ASSET missions. Also, as an active member of the International Electrotechnical Commission (IEC) I was given the opportunity to visit nuclear installations in Europe, Asia and America. In this way it was possible for me to gain an insight into the operational experiences of most reactor types. This was all crucial in helping me to write this report.
References
[1] ENS News, October 2007
www.euronuclear.org/e-news/e-news-18/HP-BWR.htm
[2] Transactions of the European Nuclear Conference (ENC) 2007, Brussels
www.euronuclear.org/events/enc/enc2007/transactions/transactions-posters-enc07.pdf
[3] ENS, April 2008, HP-BWR
www.euronuclear.org/reflections/HP-BWR.htm
[4] Transactions of the European Nuclear Society (ENS) Conference TOPSAFE 2008
www.euronuclear.org/events/topsafe/transactions/TopSafe2008-transactions.pdf
[5] Proceedings of the 17th International Conference on Nuclear Engineering, ICONE 17, July 12-16, 2009, Brussels, Belgium, ICONE17-75032
www.asmeconferences.org/icone17/
Bibliography
Nuclear Engineering International, 9 April 2009
The Best of Both, by Frigyes Reisch
www.neimagazine.com/story.asp?storyCode=2052686
Paolo Ferroni, Neil Todreas. Massachusetts Institute of Technology,
Joint Reactor Seminar University of Tokyo (GoNERI) and UC Berkeley. March 5, 2009
Improved BWR Core Design Using Hydride Fuel
Massimiliano Fratoni, Alessandro Piazza, Ehud Greenspan, University of California, Berkeley
goneri.nuc.berkeley.edu/tokyo/2009-03-12_Fratoni.pdf