
Interview with Mr François GAUCHÉ, CEA
Mr GAUCHÉ is the Manager of the Generation IV Reactors Programme at the Nuclear Energy Division of CEA, (the Alternative Energies and Atomic Energy Commission, in France). SFEN YG interviewed him on the ASTRID project (Advanced Sodium Technological Reactor for Industrial Demonstration). Here is a transcript of that interview.
Mr GAUCHÉ, could you please introduce the ASTRID project to us?
The ASTRID Project consists of the R&D, design and development of a 4th Generation Sodium Fast Reactor Prototype, with a level of safety that will be at least equivalent to the third generation of LWR and will integrate into its design the lessons learnt from the Fukushima accident.
The project involves several companies active within the nuclear industry:
-
CEA, the contracting owner, is in charge of core design
-
AREVA is in charge of the Nuclear Steam Supply System, Instrumentation and Control Systems and Nuclear Auxiliaries
-
EDF provides support and experience for the contracting owner and performs safety studies
-
Alstom Power Systems brings its worldwide expertise to bear for the design of the energy conversion part of the plant
-
Other companies are involved in various parts of the design (TOSHIBA, COMEX Nucléaire, ASTRIUM, Rolls-Royce, JACOBS France)
What exactly is a Sodium Fast Reactor?
The most widely used reactor technology uses water as a coolant, whereas sodium fast reactors (SFRs) are cooled by liquid sodium. Water slows down neutrons, whereas liquid sodium does not. That is why nuclear reactions in SFRs are governed by high speed neutrons, hence the name fast neutron reactors (FNRs). However, nuclear reactions in water-cooled reactors are, on the contrary, governed by low speed neutrons (‘thermal’ neutrons). In nuclear reactors, fissile nuclei can be split by neutron absorption into ‘fission products’, releasing at the same time both energy (used for electricity generation) and neutrons. These neutrons can either produce new fission (chain reaction), or be captured by nuclei, or leak out of the reactor.
It is a remarkable fact that, although the majority of the natural uranium – which is made of Uranium 238 – is not fissile, it can be transformed into fissile Plutonium-239 by the capture of a neutron: this is called conversion. In a thermal neutron reactor, the ratio between conversions and fission is always less than 1, thus the quantity of fissile material decreases in the reactor during the course of the cycle. In an FNR it is possible to obtain a balance between conversion and fission (‘iso-breeding mode’) or even have more conversion than fission (‘breeding mode’). Using that possibility, the spent fuel unloaded from an FNR can contain as much fissile material as when it started. Of course, uranium-238 is consumed in the process.
There are limitations due to the fission products (that hinder the chain reaction) and to the dose level that can be supported by materials like the fuel cladding. These limitations
determine the duration of the cycle, at the end of which it is required to unload the fuel, recycle the uranium and plutonium while removing the waste products, and reload new fresh fuel.
ASTRID will operate in iso-breeding mode so as to stabilize the quantity of plutonium in its fuel cycle.
FNRs can also burn so-called minor actinides, i.e. isotopes that were produced in a reactor by neutron capture of plutonium (neptunium, americium and curium). ASTRID will provide demonstration capabilities for such a process, which is also called transmutation.
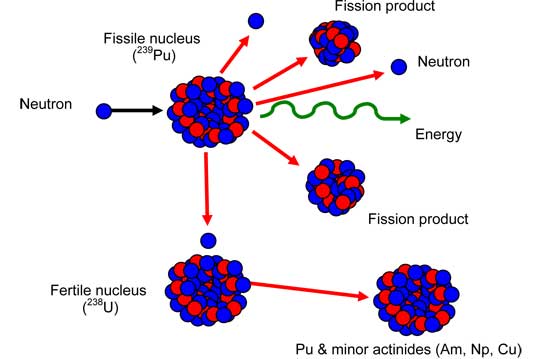
Basics of Uranium-Plutonium chain reaction within SFRs
Have such reactors already existed elsewhere in the world?
Many SFRs have already been built and operated. The most powerful SFR ever built was the French ‘Superphenix’ reactor. It was able to deliver up to 1200 MW of power to the electricity grid and was operated for 12 years. The total accumulation of the years of SFR operating experience using this technology amounts to approximately 400. Today, several SFRs are still operating, in Japan1, Russia, India and China.
What are the challenges associated with this kind of reactor technology?
Liquid sodium is harder to handle than water. Indeed, hot liquid sodium inflames in contact with air and reacts chemically when in contact with water. Not really attractive at first sight, right?
The choice of such a coolant for an FNR is based on several criteria. The first one is not to slow down neutrons. That is why water is excluded. But other key parameters (such as thermal properties, viscosity, compatibility with steel, etc.) are of the utmost importance as well. There are other possible coolants that can enable the fast-neutron reactions to take place. However, following an analysis of the advantages and drawbacks involved, and taking into account safety and operability considerations, it is difficult to find a good replacement for sodium. For example, liquid lead could be considered as a coolant instead of sodium, but one of its major disadvantages is its narrow range of operation: indeed, at temperatures above 480°C lead becomes highly corrosive for the steel that the reactor vessel, circuits and fuel cladding are made of. On the other hand, the reactor must not be cooled to less than 400°C to ensure that lead does not freeze in the circuit. So the compulsory temperature range of the reactor at all times would be between 400 and 480°C, which is not that comfortable, e.g. for maintenance in a “cold” state. In order to widen that 80°C range, bismuth can be combined with lead to lower its freezing temperature. Unfortunately, when subjected to radiation bismuth is transmuted into Polonium-210, which is a highly radiotoxic isotope.
Alternatively, instead of liquid sodium, a gas might be used, like helium. However, gases have a low thermal inertia, which means that these types of reactors are sensitive to depressurization. Safety demands that high margins be taken and that materials that can withstand up to 1600°C be used: this technology is not available today and will need significant R&D before proof of its feasibility can be obtained.
These two examples show that there is no such thing as the “perfect” coolant. The weaknesses of sodium are well-known and engineered barriers can be designed to control them, so that as a result of a multi-criteria analysis, sodium is considered worldwide as the reference choice for FNRs.
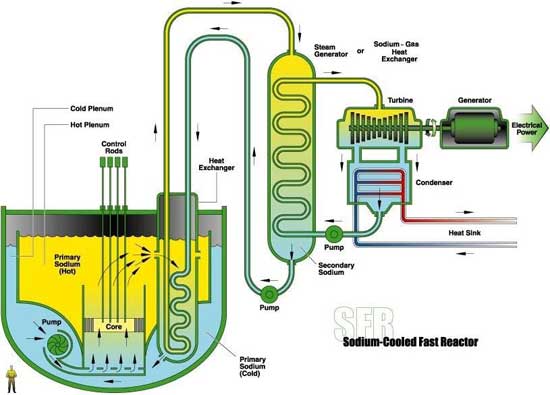
Circuits in a Sodium Fast Reactor
How does the ASTRID project cope with the requirements for safety?
There are three main issues to deal with here: air-sodium fires, sodium-water reactions and a more technical issue known as “positive void-coefficient”. In order to avoid sodium fires resulting from its coming into contact with air, on top of design provisions and quality control of the piping, the rooms where sodium circuits are located can be filled with nitrogen instead of air. Moreover, the vessel is made of three layers: the main steel vessel is contained in a safety steel vessel, which is in turn contained in a concrete vessel-shaped pit with a steel-liner. The “pool-type” reactor design benefits from a fully integrated primary circuit, i.e. all the equipment is contained in the vessel, instead of drawing pipes out of the three-layer vessel. That makes the reactor mechanically stronger and provides the guarantee that the sodium cannot physically escape from the primary circuit.
In classical designs where steam generators feed steam to a conventional turbine connected to an electrical generator, sodium-water reactions can occur and need to be addressed. To make sure the consequences of such a sodium-water reaction do not affect the primary circuit, one possibility is to limit the size of the steam generators (modular steam generators). They are installed on a so-called ‘intermediate circuit’, which is a second sodium circuit used to provide an additional barrier between the primary circuit and the environment, so that the water-sodium interface, located in the steam generator between the intermediate circuit and the water circuit, is far away from the nuclear material. Another more radical solution currently being studied is to replace the water with a different liquid - pure nitrogen for instance. There is also one more drawback to using sodium: contrary to most water-cooled reactors, SFRs’ void-coefficient is positive in classical designs, which means that in case of the coolant boiling the core reactivity increases and leads to a power excursion. To avoid that, the shape of the core for ASTRID has been designed to get a very low or negative void-coefficient and thus to avoid the power excursion in case of a loss of cooling accident: this is a major safety improvement compared to previously designed SFRs.
Once the issues have tackled, what are the advantages of sodium?
‘Pool-type’ SFRs have a thermal inertia combined with a boiling margin around 20 times greater than that for water-cooled reactors. That is of great help in accident studies: in the case of a loss of reactor cooling, the low kinetics of the accident increases the ‘grace period’ required to take the necessary actions to bring the plant back to a safe state and to avoid severe accidents such as reactor core meltdowns.
Another good point is that the operating temperature of SFRs is around 550°C, which allows considerable heat exchanges with air. Thus, the heat sink, usually a sea or a river, can be diversified: in case of loss of the main heat sink, dedicated safety systems transfer the heat directly to air via dedicated heat exchangers. Such systems can be designed as passive systems operating under natural circulation (heated sodium going up, and cooled sodium coming back down) is quite efficient in SFRs. This passive feature is of course very interesting within the context of post-Fukushima studies as the focus on studies of total loss of electrical supply increase in importance.
Unlike PWRs, which are pressurized at 155 bar, SFR vessels are almost at atmospheric pressure: this eliminates by design pressure-related loss of coolant events.
Finally, one of the greatest assets of sodium is that we have 400 years of cumulated experience of operating with it. So, we know its strengths, for example that it can be used for instance to design efficient safety systems, and we also know its weaknesses for which we can design dedicated engineered barriers. Let us not forget that safety is improved by learning lessons from our experiences.
What is the point of developing a new reactor technology?
This comes from the need to make better use of and recycle nuclear materials like uranium, plutonium and minor actinides. Natural uranium is composed of two isotopes: Uranium-238 is present at 99,3%, and Uranium-235 accounts for the remaining 0,7% of natural uranium. Water-cooled reactors - like the 58 reactors currently in operation in France - mostly ‘burn’ Uranium-235 out of fuels made of enriched uranium. Even if another type of fuel can be partially used (MOX fuel, i.e. plutonium-uranium oxide), this means that a maximum of 1% of the energetic content of natural uranium is used, leaving the majority remaining part in the form of depleted uranium or reprocessed uranium. During the enrichment process, the percentage of uranium-235 is increased in the fuel, leaving aside depleted uranium. For example, in a typical open cycle for a 63GWe fleet, the enrichment of 9,600 tons of natural uranium leaves 8,400 tons of depleted uranium aside containing almost only uranium-238. On earth there are 189 billions tons of oil, 187 Tm3 of Natural Gas, 860 billions of tons of coal2 and 4 million tons of natural uranium3. If we consider that uranium is used only in thermal neutrons reactors, converting these stocks into energy reveals the following chart:
Total energetic contents of various sources of energy according to confirmed stocks
Purple: Coal / Pink: Oil / Orange: Natural Gas
Green: Uranium in Thermal Neutrons Reactors
This uranium-238 cannot be used in water-cooled reactors but could be used in FNRs, multiplying the energy content of uranium by a factor of more than 100. Thus the chart changes as follows:
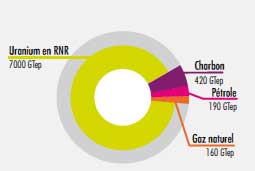
Total energetic contents of various sources of energy according to confirmed stocks
Purple: Coal / Pink: Oil / Orange: Natural Gas
Green: Uranium in Fast Neutron Reactors
Global reserves of uranium-235 (the 1%-part) could be exhausted in less than a century if the rate of use follows the current trend. On the contrary, global reserves of coal are high enough to let coal power plants be operated for centuries, which could lead to an environmental disaster. However, for the nuclear reactions that take place in SFRs the exhaustion of uranium-238 used in these reactors is forecast as being after several millennia of electricity consumption! On top of that, due to uranium enrichment activities, several countries already own great amounts of depleted uranium, France included. This depleted uranium can be used to fuel SFRs, enabling the uranium supply to be secured.
As far as CO2 emissions are concerned, SFRs stand out as being millennium-sustainable, economically viable and a carbon-free source of energy.
France has a leading position in the nuclear energy industry due to its considerable experience and its high safety standards. Consequently, it has a duty to keep an eye on the required long-term strategy. If France does not get involved in the future of the nuclear industry, other countries will take the lead and their safety standards might become global standards, for better or for worse. General consensus dictates that we do everything possible to stop emitting greenhouse gases. That is why the future of nuclear energy must be developed now, by countries that have experience and credibility as regards progressively improving nuclear safety.
What are the milestones of the ASTRID project?
At the end of 2012 the first phase of the conceptual design was completed. The main safety features of the reactor were presented to the French Nuclear Safety Authority in a document sent in June 2012. Within three years, a major document, called the Safety Options File will be written. It will bring together all the strategic guidelines and rules governing reactor design. Thanks to this document, the basic design of the reactor will be carried out, leading to the writing of a Preliminary Safety Analysis Report, in 2019. First criticality could be achieved in 2025, so that the operation of ASTRID provides sufficient feedback of experience for commercial deployment from 2040.
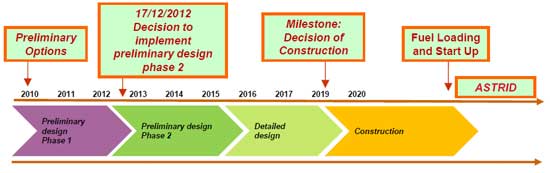
ASTRID project schedule
What is your motivation for delivering a programme with such a long timeline?
This programme is not meant to optimise short-term profit. It is meant to prepare the future of energy sources. I strongly believe that centralized, intensive energy sources are needed, and that nuclear energy can continue to give our country a competitive advantage. In a few decades, thanks to the ASTRID project, economic, sustainable and carbon-free energy sources will be available that will prevent the release of greenhouse gases. This is the reason why I am involved in the ASTRID project.
An interview conducted by Fadhel Malouch and Charles Michel-Lévy of the SFEN YG
1 After the Fukushima accident, the future of Japan fast neutron reactors remains uncertain
2 Source : BP statistical Review of World Energy, June 2011
3 Source : Red Book, 2009 edition (RRA)
|