INDUSTRIAL APPLICATIONS
Enhancing Product Quality
Sensitive, accurate and reliable control systems are
essential to industry. Nucleonic gauges – instruments that use a radioisotope source to measure materials
and products – can improve product quality, optimise industrial
processes and save energy and materials. They are extremely sensitive,
and often succeed where other methods fail.
Nucleonic gauges are ideal for arduous or dangerous industrial environments, including
high-temperature and high-pressure situations. They are also non-invasive
– no physical contact is required between the sensor and the material
– thus quality checks can be performed on-line during production.
Sizeable financial benefits can be realised from the reduction of scrap
and waste and the assurance of high quality products that retain customer
loyalty.
The metal-coating industry uses nucleonic gauges to ensure optimum coating thicknesses. Moisture gauges are essential in industries involving construction
materials, glass, mineral processing, chemicals and food. Radioisotope gauges, used to measure mass per unit of area –
often at high speeds – are indispensable in manufacturing aluminium
foil, paper and steel plate.
Advanced Materials: Exceptional Properties
Many industries are now demanding higher-performance
polymeric materials at lower cost. Radiation is proving
to be a valuable tool in polymer processing, and the IAEA is assisting
many developing countries in expanding their use.
Gamma and electron beams can induce beneficial properties
in plastic or polymeric materials and have been used for decades in
developed countries. Radiation can cause cross-linking of some molecules
to form giant molecules which have higher heat, chemical and mechanical
resistance. It can also degrade some plastics, reducing them to a powder
that can be used as an industrial lubricant.
The wire and cable industry uses cross-linking to strengthen
the insulation of wires and cables and make them more heat resistant.
The pliable plastic is extruded, and then radiation cross-linked to
harden it.
Radiation vulcanisation of natural rubber latex (RVNRL)
imparts strength and elasticity, making it ideal for the production
of surgical gloves, catheters and balloons used in cardiac procedures.
RVNRL also results in people-friendly products that are free of allergy-causing
residues.
Non Destructive Testing
It is essential to test some materials, products, engineering
structures or buildings without altering their properties or affecting
their usefulness. Non-destructive testing (NDT) comes in many forms,
one of the most popular being radiography, which uses a radioisotope
or X-ray source. NDT radiography is used extensively in the petroleum,
chemical and nuclear industries, as well as on assembly lines to test
consumer goods. Light alloy castings, such as car wheels, receive a
quality check of this type before leaving the factory. Pipelines, too,
are prime NDT candidates – both during installation and maintenance
- to ensure that welds remain intact.
In NDT radiography, gamma rays from a sealed source or X-rays are directed through the object, and
the results shown on film or other media. Imperfections are indicated
as the density changes – just as a body X-ray reveals broken bones.
A recent development is real-time radiography, where faults can be evaluated
on a computer screen for assembly-line inspections and troubleshooting.
|
|
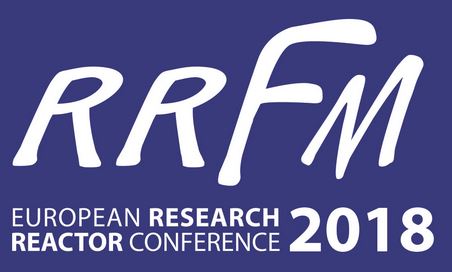
11 - 15 March 2018
Munich, Germany
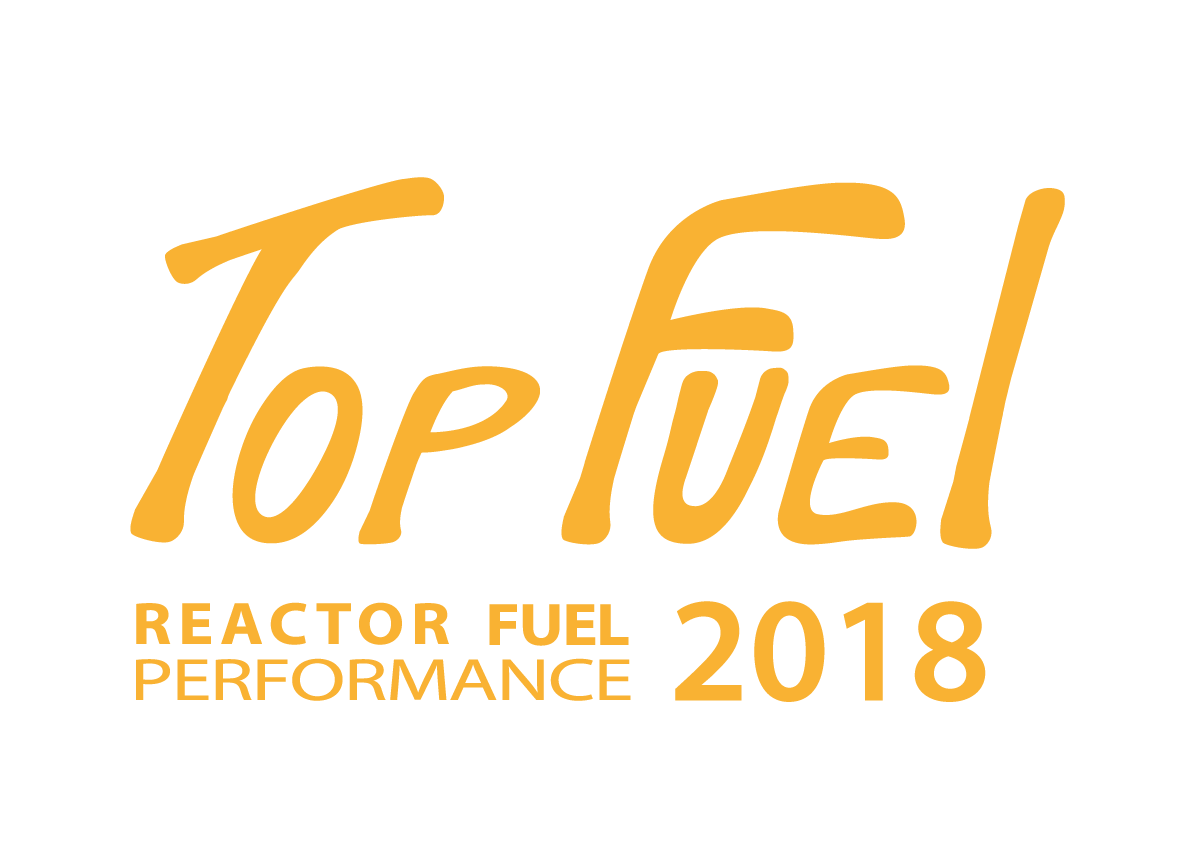
30 September - 04 October 2018
Prague, Czech Republic |