
Excursion of Czech Young Generation to the manufacturing
facilities of ŠKODA JS (Nuclear Engineering) in Pilsen
By Lukáš Nesvadba, Martin Precek, Markéta
Somolová
On 1 April 2007, an overcast morning and bitingly
cold wind has chased one’s hands into the safety of warm
pockets. In spite of this ten intrepid Czech “youngsters”
met at 8.30 at the entrance to the Škoda JS factory –
at Bolevec near the famous Czech city of Pilsen. We were welcomed
there by Dr. Václav Bláha, Vice President of the
Czech Nuclear Society, who was our guide throughout the visit
to Škoda JS that day.
First we were introduced to the history of the
Bolevec area. At the turn of the 19th and 20th
century it served as a testing ground for all kinds of weapons
that the Škoda company manufacturzed. Even by now there are
supposed to be unexploded munitions buried below several meters
of ground somewhere in the area. It started being used for the
nuclear industry in the second half of 20th Century.
Škoda JS is in fact the successor of the company Power Plant
Construction, which was founded in 1955 and has played a key role
in the development and construction of the Czechoslovakian design
heavy water moderated and gaseous CO2 cooled power
plant, A1, in Jaslovské Bohunice (150 MWe, operational
between 1972-1977 and closed due to an accident classed 4 on the
INES scale). Later on it also played a significant role in the
construction of Soviet-type light water reactors (WWER) that were
used all over central Europe. At present, the main operations
at Bolevec are concentrated in two buildings –the so called
“Light Hall” and the Experimental Hall.
In the Light Hall we were greeted by the Head
of Operations, Miroslav Hejda, who explained the origins of the
Hall’s name – the word “light” refers
to its manufacture of products weighing less than 5 tons. At present
these are namely linear step drives for control organs for reactors
WWER-440 and WWER-1000, pins for carrying the CASTOR spent fuel
containers and the non-nuclear parts of the nuclear fuel for WWER-1000
(fuel assembly heads and bases) for Westinghouse. The Light Hall
was built 15 years ago and it is a very modern factory. The construction
material used for most of the products is austenitic steel precisely
machined on numerical-controlled lathes. Machined parts are then
welded on special workplaces. Pride of place in the factory goes
not only to the Japanese NC-lathes “Mazak”, but also
to a device for electron-beam welding. Surfaces of the welded
metal joint are heated inside a vacuum chamber under bombardment
by electrons that are accelerated by 60 kilovolts at currents
reaching up to 250 milliamperes (the maximum input is, therefore,
15 kW). The process can be seen through a lead-glass partition
to protect staff from fast electron induced X-rays. This clean
way of welding without any additional welding components makes
it possible to weld parts up to 4 cm in depth (from one side –
welds from both sides allows welds of up to 8 cm deep). It masters
the welding of most metals and is very useful for welding high
carbon-content steels (max. 22 % C). However, it can not weld
zinc as it quantitatively evaporates in the combined high temperature/low
pressure conditions. After welding the products are transferred
into the assemblage hall, where they are de-greased and tested
for flaws – especially their welds. The employed testing
techniques include¬ ultra-sound, X-ray and magnetic fluorescence
analyses. At the end of the process the finished products are
displayed on stands prepared for the customer.
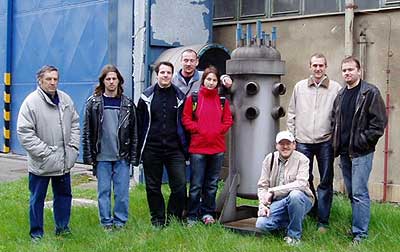
Czech YG members assembled in front of the Škoda
JS Reactor Hall, around a symbolic model of a VVER-440 reactor
vessel that was produced there on many occasions.
Next Dr. Bláha showed us the Experimental
Hall which was originally used for the gas cooled programme of
the heavy water moderated A1 reactor. Because of its earlier function
it is no less than 24 meters high to be able to house the long
gas channels. However, the gas programme was cancelled (not only
due to political reasons) in 1968 and, in connection with the
light-water programme, a water-circuit adapted to the parameters
of a WWER-1000 reactor was installed there. It has been used,
e.g., for testing control rod drives under real operation thermo
hydraulic conditions. In addition to the water loop, an independent
sodium loop was installed in the Experimental Hall as part of
the fast reactor research programme, but it never actually was
operational. In the 1990s, hexagonal fuel assemblies made by Westinghouse
for the Temelín NPP (2 x WWER-1000) were intensively tested,
particularly for heat-transfer crisis – a phenomenon that
causes rapid fall of heat-transfer from the over- heated fuel
rod to the cooling medium due to the formation of a thin vapour
film on the surface of the cladding. New tests are currently being
planned in connection with the change of the Temelín NPP’s
fuel supplier from Westinghouse to the Russian firm TVEL.
After visiting the Experimental Hall we headed
south by car from the wooded Bolevec area into the factory-grounds
of the originally jointly-owned Škoda company, which is located
in the Pilsen city centre. Within the cluster of factory buildings
the companies that took over from the old machinery-making giant
are located. As we made our way through the labyrinth we passed
the main factory of Škoda POWER, which manufactures turbines.
However, we were also interested to visit Škoda JS’
second key manufacturing plant – the Reactor Hall. Head
of Operations, Miroslav Nolc, explained that the building is 27
years old and its 40 meters tall and that the lifting-capacity
of the strongest crane is 400 tons. In the past, the Hall produced
WWER 440 and 1000 reactor vessels, but after the completion of
Temelín NPP the nuclear programme slowed down and production
was focused temporarily on reactor vessels for the chemical industry
(with no lower requirements, one chemical reactor for ammonia
production could run tests under a pressure about 50 MPa) and
for CASTOR spent fuel containers.
As we passed through the Reactor Hall, we could
see that production was devoted exclusively denoted to the nuclear
power industry, because Škoda JS has been successful on the
markets of Western Europe. IN addition to the production of CASTOR
transport containers (the older type) for the Obrigheim NPP (Germany),
we saw production linked to that “symbol of European nuclear
renaissance” – the European Pressurized Reactor for
Olkiluoto 3, in Finland.
Although the number of CASTOR containers being
manufactured was high (in total 15), all the production process
steps were demonstrated at each individual work-station. The 120
ton steel-iron cast in the form of a hollow cylinder that is closed
at the bottom is supplied by the steel foundry of the Škoda
Steel company. It is machined by first cutting inner steps for
two hermetical lids. Vertical sample-drills are then made through
the container walls (to test the metal’s homogeneity). If
the analysis yields positive results, the whole diameter of the
container is drilled with long vertical holes, in which special
polyethylene rods will be inserted to slow down the fast neutrons
arising from the spontaneous fission of higher transuranic elements
contained in the spent fuel. After preparing the places where
the carrying-pins are inserted, the flat surface of the cylinder
is machined into characteristic ribbing to allow better heat-removal.
Once all the mechanical adjustments have been made, the vessel
is then galvanised with a 3-millimeter thick layer of nickel (during
this process the vessel is filled with an electrochemical nickel-solution)
for 7 days. After the internal nickel coating, the external surfaces
are shot-blasted in a special container with an abrasive powder
stream (and, therefore, de-greased) in order to make the protective
varnish paint - which was blue in this case - stick better to
the surface. Apart from the CASTOR containers, CONSTOR containers
for the Lithuanian NPP Ignalina are also made in the Reactor Hall.
These containers are different insofar as they are not just metal
- the hollow space inside the metal double wall is filled with
concrete.
The Hall has a variety of giant milling cutters
and drilling machines for machining the metal products. We were
primarily told that the boring mill schies capable of work with
up to 10 meters large objects and about a giant automated welding
machine (using welding flux). The machining modifications create
mechanical stresses that have to be removed by heating –
which is done inside one of the two giant electrical furnaces
that reach temperatures of up to 800°C.
AREVA has chosen Škoda JS as a supplier
for the internal parts of the EPR reactor vessel (European Pressurized
Reactor, 4500 MWt, 1600 MWe). In the Reactor Hall we had, therefore,
a chance to stand inside the steel neutron reflector of the squared
reactor core – at that time it contained stacked, un-welded
rings. We saw the inner reactor barrel and we observed the very
slow circular precision grinding process carried out by one of
the control rod stabilizing grids. In addition, we were also shown
the welding of the reactor-supporting ring. The reactor pressure
vessel itself is being manufactured in Japan, because the stringent
requirements for low number of metal welds of such a great vessel
increases the minimum metal ingot weight to levels that can be
met only by the steel-works of Mitsubishi Heavy Industries.
We would like to give a special vote of thanks
for the successful organization of the trip to Dr. Bláha
and the Škoda JS company as the last part of our excursion
in Pilsen was not to the Škoda factory but to the world-famous
Plzenský Prazdroj a.s. brewery (although its name is more
popular in its German version - Pilsner Urquell - that can be
roughly translated into English as "The Headspring of Pilsen.").
In the brewery, founded in 1842 as “The Citizens’
Brewery of Pilsen”, a professional guide – Mr. Hála
– gave us a tour around the brewery and showed us roughly
how Pilsner Urquell beer is brewed. He led us from a very nice
Info center through a small gate into the factory itself. There
a small mini-bus took us to the most modern part of the factory
that was finished only this year – a bottling plant with
a surface area of 2000 square meters! In this great hall, which
cost over 1 billion Czech Crowns (35 million €) to build,
there are lines for the control & removal, washing and filling
of glass bottles (plus an extra one for filling alluminium cans,
of course). The glass bottles are removed and re-melted after
3 or 4 cycles between the brewery and its customers. The bottling
plant can produce over 60 thousand bottles a day, even though
more than half of its space is no longer used and is awaiting
possible expansion. In fact, only some of the bottles are filled
with Pilsner Urquell beer. The plant also bottles other beer brands
produced by breweries belonging to the Pilsner Urquell group (Gambrinus,
Radegast and Velkopopovický Kozel).
Next we passed by an array of tall vertical cylindro-conical
fermenting tanks, where the beer maturing process takes place,
and the historical 46 meters tall water tower. Then we visited
the newly-built brewery where the giant copper and stainless-steel
kettles contain the “mash” (mixture of water and crushed
barley malt) that then forms a fermentable liquid called “wort”
(a water mixture of simple sugars generated by boiling off the
starch from the barley grains). This is that is then mixed and
boiled with hops, which give the beer its characteristic taste.
Finally, we visited the underground part of the
brewery, which is not used nowadays except for a very small part
where the company has preserved the historical way of maturing
beer in cold cellars in wooden tubs and barrels. Under the brewery
are large underground cellars that were mined out during the 19th
Century. They once housed around 6 000 wooden barrels containing
up to 30 or 40 hectoliters. The fresh (so called “green”)
beer produced by 1 week of fermentation in opened tubs at temperatures
slowly rising from 5 to 9 °C had been transferred into the
great barrels, where it slowly matures into its final form over
several months. When the maturing process is over, the beer was
transferred into small beer barrels and distributed all around
the country to the local pubs. At present, the brewery has 13
fermentation vats and 90 oak barrels – we were invited to
test a specimen of this historical beer, which is different from
the contemporary beers by its significant content of beer yeast.
All presently mass-produced beers are filtered from the yeast
(since the beginning of 20th century) and pasteurized (since the
end of the Second World War). So, it was a memorable ending to
a long day.
|