
CONCEPT OF A FUTURE
HIGH PRESSURE - BOILING WATER REACTOR,
HP-BWR
F. REISCH
Department of Nuclear Power Safety, KTH, Royal Institute of Technology
Alba Nova University Center Roslagstullsbacken 21, SE-106 91, Stockholm – Sweden
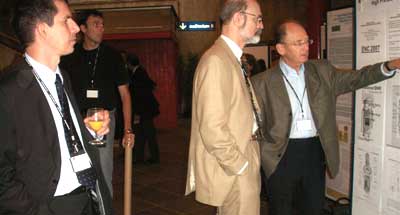
ABSTRACT
Some four hundred Boiling Water Reactors (BWR)
and Pressurized Water Reactors (PWR) have been in operation for
several decades.
The present concept, the High Pressure Boiling Water Reactor
(HP-BWR), makes use of this operating experience. The best
parts of the two reactor types are used and the troublesome components
are left out. This means improved safety. The increased thermal
efficiency is beneficial to the environment as less cooling
water is released per produced kWh. With some modifications
the used components can be used to make this design
cost
effective and possible to achieve in the currently not too distant
future.
1. Introduction
Since the 1950s several hundred
Boiling Water and Pressurized Water Reactors (BWRs and PWRs)
in use. There is a wealth
of operating experience. During this have been time many difficulties
occurred with a number of important components. This concept,
the High Pressure – Boiling Water Reactor (HP-BWR) offers
a solution to use the best parts from each type (BWR and PWR)
and leave out the troublesome components. This means an important
increase of safety. As an extra benefit, also increased efficiency
attained beneficial for the environment as less cooling
water is released per produced kWh. The HP-BWR is using –with
some modifications- currently manufactured parts making this
a cost effective, realistic concept.
2. The High Pressure – Boiling Water Reactor HP-BWR
The High Pressure Boiling Water
Reactor (HP-BWR) offers improved nuclear safety and less damage
to the environment. The HP-BWR is an environmentally friendly,
effective alternative.
The High Pressure- BWR
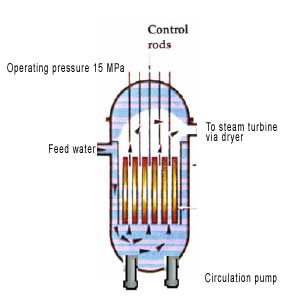
The HP-BWR uses a modified PWR reactor vessel
and BWR type fuel and control rods. However, here the cruciform
control rods are gravity operated with ample space between the
crosses and the fuel boxes. The control roads are manoeuvred
electromagnetically, which means that they will drop into the
core when there is a loss of electrical power as in the PWRs.
The traditional PWR control rods are finger shaped and are surrounded
by a tube
with a minimum of clearance. The traditional BWR control rods
are operated from below with hydraulic pressure. Therefore, at
the bottom of the traditional BWR reactor vessel there are
a
great number of penetration points for the control rods. Directly
below the reactor vessel there is an elaborate system of numerous
high
pressure hydraulic pipes to actuate the control rods. Taking
the best fro and leaving out the drawbacks of both the traditional
BWR and PWR systems is a substantial safety improvement.
All the pipe connections to the reactor vessel
are well above the reactor core. This allows the omission of
core spray. The moisture separators and steam dryers are
outside the reactor vessel, leaving free space for the control
rods.
Internal circulation pumps. These allow the
use of orifices at the inlet of the fuel boxes so that the one-phase
pressure drop will
predominate over the two-phase pressure drop. This reduces the
risk of hydrodynamic oscillations. However, if suitable methods
are
found to facilitate natural circulation even the circulation
pumps can be left out.
The use of the HP-BWR means improved Carnot
cycle thermal efficiency up to about ~40% instead of about ~30%.
The reason is that the
HP-BWR steam temperature corresponds to 15MPa while the traditional
BWR’s steam temperature corresponds to 7MPa and the traditional
PWR’s steam temperature corresponds to 6MPa. The HP-BWR
is lenient to the environment as less damaging cooling water
is released per produced kWh to the recipient, sea or river or
to
the air
via a cooling tower.
Using direct cycle the system is simplified. Still, the usual
PWR steam lines can be used through the containment wall to the
turbine. A great advantage is that the complicated and costly
steam generators are left out.
The moisture separators and the steam dryers are outside the
reactor vessel in the containment instead of the huge troublesome
steam generators.
Simple dry containment is used instead of the complicated, inert,
pressure suppression wet containment which requires a great deal
of surveillance.
3. The Traditional Boiling Water Reactor, BWR
The basic principles of the traditional Boiling Water reactor
are well known Traditional BWR
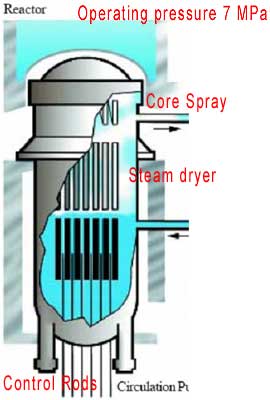
As there are pipe connections to the
reactor vessel below the reactor core, a pipe break can empty
the vessel leaving the core uncovered, without the cooling water.
Therefore, a core spray is required. This is a common feature
for the BWRs with external circulation pumps or jet pumps. However,
this draw back is eliminated at a later design stage with the
Advanced Boiling Water Reactor, ABWR. All BWR control rods are
inserted
to the core using hydraulic power; some with electric motors
too. This makes the lower part of the rector both inside and
outside
the bottom of the reactor vessel extremely elaborate. To make
things worse, in the past, cracks, corrosion and leakage occurred
at the penetrations at the lower part of the reactor vessel.
Structural sketch of reactor pressure vessel
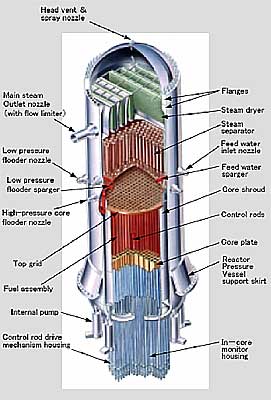
Traditional Advanced Boiling Water Reactor (Hitachi–ABWR)
The huge reactor vessel would require an enormous
dry containment building. Therefore, a pressure suppression
containment system is used instead. The containment is separated
into two parts, the upper dry well and the lower wet well with
the
suppression pool. If the separation is not perfectly leak-tight
the wet well cannot fulfil its function to suppress the pressure
in the dry well in case of a pipe break. Further complication
is that the traditional BWR containment operates inertly, making
difficult the entrance into it.
The nice thing about the BWR is that it operates
in direct cycle mode without the troublesome steam generators.
4. The Traditional Pressurized Water Reactor,
PWR
Most of the world’s operating
reactors are traditional PWRs.
Traditional BWR
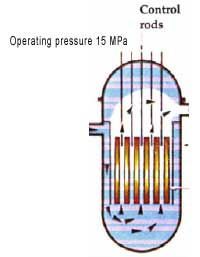
The control rods are operated from above. Undoubtedly
some leakages were observed at the penetrations which in a few
cases led to the need to replace the reactor pressure vessel
head. Reactor Concept Manual - Pressurized Water Reactor
Systems 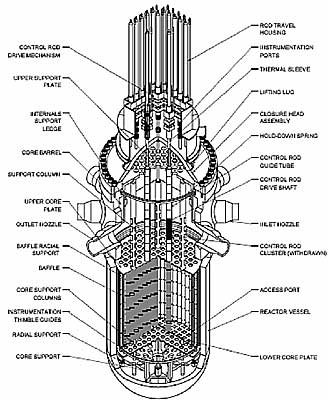
The simple electromagnetic devices which manoeuvre
the rods worked reliably. This assures a high degree of safety.
A basically continuous, uninterrupted bottom of the reactor vessel
avoids any suspicions of its integrity.
Cutaway View of Reactor Vessel
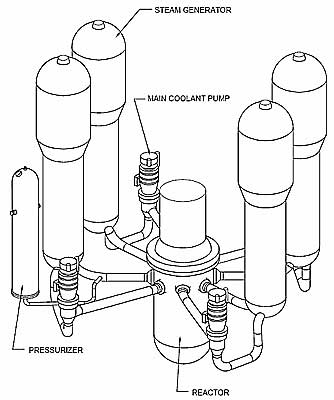
A four-loop Westighouse plant has four steam
generators, four reactor coolant pumps, and a pressurizer.
The four-loop units in the United States are Braidwood 1 and
2, Byron 1 and 2, Callaway, Catawba 1 and 2, Comanche Peak
1 and 2, D.C. Cook 1 and 2, Diablo Canyon 1 and 2, Indian Point
2 and 3, McGuire 1 and 2, Millestone 3, Salem 1 and 2, Seabrook,
Sequoyah 1 and 2, South Texas Project 1 and 2, Vogtle 1 and
2, Watts Bar 1, and Wolf Creek. Each of these plants has 193
fuel assemblies arranged inside a reactor vessel that has an
internal diameter of 173 inches (except South Texas has an
internal diameter of 167 inches). The fuel assemblies are arranged
in 17 x 17 array except for Cook and Indian Point, which have
15 x 15 fuel. The electrical output of these plants ranges
from 950 to 1250 megawatts.
The curse of the traditional PWRs is their
steam generators. These complicated and costly huge pieces
of equipment are disappointingly short lived because of the
corrosion of the internal tubes, which can cause leaks.
The plant owners used to change them after some fifteen years.
An extremely
expensive and troublesome and also time consuming operation.
Steam dryer in a SG
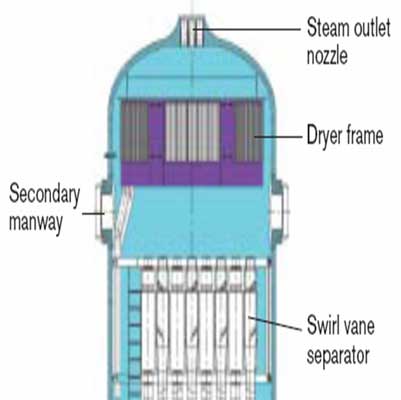
In the upper part of the steam generators
there is the moisture separator and the steam dryer. The HP-BWR
is “borrowing” this equipment which can be used
without the troublesome steam generators.
5. References
All university text books written for nuclear
engineering students contain detailed descriptions of both
Boiling Water
Reactors and Pressurized Water Reactors. Also manufacturers
in Europe, Asia and America publish data about their
designs. There is also a wealth of information about BWRs and
PWRs on the internet.
download
Presentation
|