
Two Phase Flow
Test Loop Results for BWR
Frigyes Reisch
Nuclear Power Safety, KTH, Royal Institute of Technology
Stockholm, Sweden
Seminar
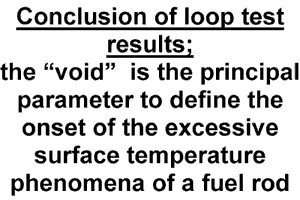
Normally
the fuel surface is effectively cooled by boiling water. However
if the heat flux exceeds a critical value the heat transfer from
the fuel surface into the coolant deteriorates, with the result
that drastically increased fuel surface temperature occurs.
According to Michael L. Corradini University of Wisconsin, Madison
WI the
"mechanisms of critical heat flux" are:
a) Formation of hot spot under a growing bubble,
near-wall bubble crowding and inhibition of vapor release. Here,
when a bubble grows at the heated wall, a dry patch forms underneath
the bubble as the micro-layer of liquid under the bubble evaporates.
In this dry zone, the wall temperature rises due to the deterioration
in heat transfer.
b) Near-wall bubble crowding and inhibition
of vapor release: here, a 'bubble boundary layer' builds up
on the surface and vapor generated by boiling at the surface
must
escape through this boundary layer. When the boundary layer becomes
too crowded with bubbles, vapor escape is impossible and the
surface becomes dry and overheated, giving rise to burnout.
c) Dryout under a slug or vapor clot. In plug
or slug flow, the thin film surrounding the large bubble may
dry out giving rise to localized overheating and hence burnout.
Alternatively, a stationary vapor slug may be formed on the wall
with a thin film of liquid separating it from the wall; in this
case, localized drying out of this film given rise to overheating
and burnout.
d) Film dryout in annular flow. Here, in annular
flow, the liquid film dries out to evaporation and due to the
partial entrainment of the liquid in the form of droplets in
the vapor core.
Excessive fuel temperature can be caused e.g.
by overpower or reduced coolant flow. With neutronics and thermal-hydraulic
power oscillations when the duration of the power peaks are very
short temporary over temperature can occur without causing fuel
failures as the normal cooling can quickly recover.
To avoid excessive fuel temperature, the knowledge of the onset
of the overheating phenomena is absolutely necessary, both at
the design stage and for the safe operation of a reactor. There
are complex correlation especially developed for specific fuel
bundle designs. These correlatoins are containing; surface power,
mass flow, system pressure and other parameters. While analyzing
recent test results it was recognized that a single parameter
the void is characterizing the onset of the overheating phenomena.
CHF (Critical Heat Flux) Mechanisms
Figure 1. Critical Heat Flux
Mechanisms
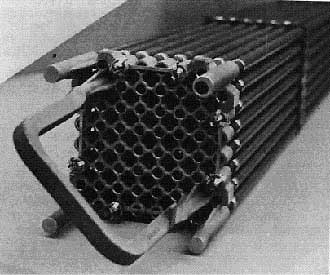
BWR fuel spacer
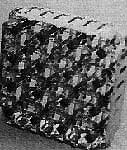
Measurements
have been carried out in a two-phase flow test loop consisting
of two heated concentric tubes, the central one representing
a fuel rod while the outer pipe emanates the heating power corresponding
to the surrounding fuel rods in a reactor core. This loop has
been in operation for some thirty years to simulate thermal hydraulic
conditions in Boiling Water Reactors. A wealth of data has accumulated
during this time and has helped to enable BWRs to be operated
safely and
economically.
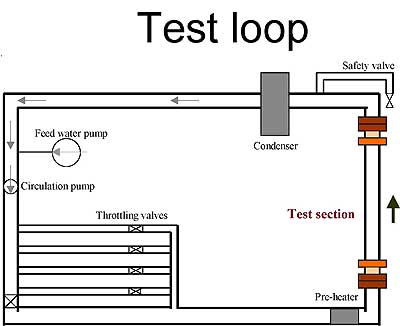 Test
loop cross section
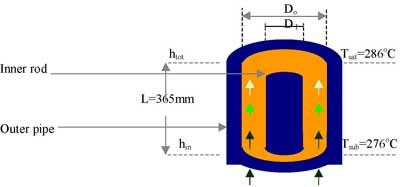
The results of the recent tests were studied
to investigate the occurrence of the onset of the excessive temperature
on the surface of the inner - and outer test tubes in htis annular
flow system. The test covered the pressures of 30, 50
and 70 bar; sub-cooling 10° C and 40°C; mass velocities
between 250 and 2250 kg/m2s and a total input power
up to 580kW with uniform power distribution. The tests have been
repeatedly performed with pin spacers, and 7 and 6 grid spacers.
Then the test results were evaluated. To calculate
the steam quality, the continuity - i.e. the heat and mass balance
equations were applied. To calculate the void three known slip
correlations; Kirilov, Thom and Zivi were used (Fig.1). Kirilov
is the most recent one. The most important result is, that
at the onset of the excessive surface temperature the void value
changes
merely between 0.88 to 0.99, while the steam quality changes
in a wide range from 0.45 to 0.75 (Fig.2). This means
that the occurrence of the onset of the excessive surface temperature
is basically dependent on the void. The performed analysis shows
the same results regardless which correlation is employed and
are valid at all the actual pressures, subcooloings,
mass flows, spacer types and their positioning along the test
section. There
has been an awareness of this however - according to the author
- but it has not yet been explicitly outlined. This
help to focus on the void when planning furher test loop experiments
as well as when monitoring the safety of operating reactors and
fuel design.
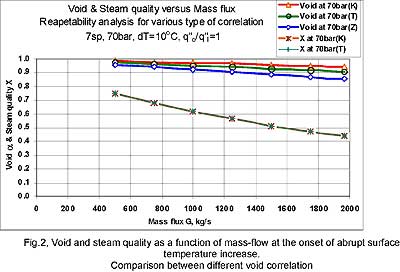
The awareness of this result helps with the
design of a tool to avoid excessive fuel surface temperature
and clad failure in operating reactors. To monitor the void during
operation
is not feasible, however from the measured parameters, power,
power distribution, coolant flow, pressure etc. the steam quality
everywhere in the core can be calculated
continuously and the void can be deduced using steam quality
versus void correlation from loop experiments. By using the constraints
described here - limiting the permissible void content - damage
of the fuel can be avoided.
Curiously it can be noted that an analytical
model is described in the DOE rapport KAPL-P-000160 by Alajbegovic,
et.al. The mathematics are applied for a Freon loop and the deduced
figures coincide with the measurements from the experimental
loop. The results are summarized in Figure 3. The abrupt increase
of the temperature here too occurs when the void value reached
around 90%.
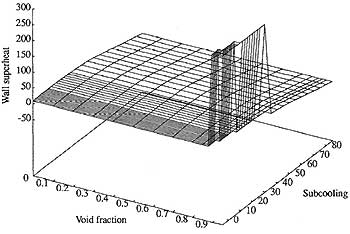
Figure 3. Prediction of critical
heat flux for Freon at p=1.5 bars, q ”= 190 kW/m2 at
constant liquid velocity of 0.5 m/
|